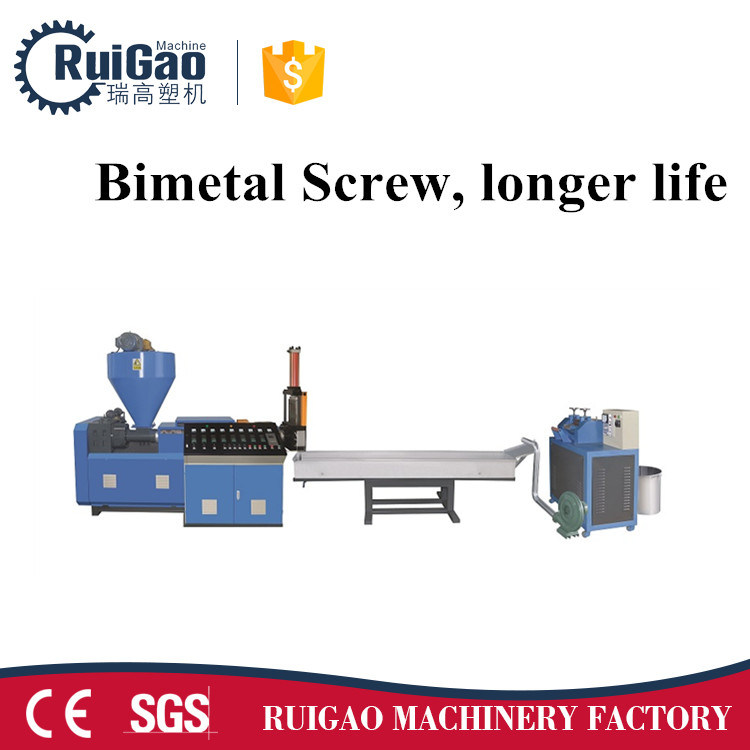
1. Machine Introduction
Plastic Recycling Machine  is suitable for regeneration and granulation of waste plastics, such as HDPE, LDPE and PP &PET etc.
It's equipped with quick motor-operated filter-screen-replacing unit and automatic temperature control.Â
The granulating crusher uses adjustable speed synchronously.
Â
Â
2. Machine Advantages
1, Screw and barrel is nitrided by 72 hours. 38 chromium materials,  it is very hard.
2, Motor with CE standard, more than 10 years life.
3, Hard surface gearbox, the life can be more than 5Â years.Â
4, Electric parts is CHINT, the best supplier in China.
5, The screen changer is by electric controlling, you can choose hydraulic controlling.
6, Water tank is stainless.
Â
3. Machine Parameters
 Model |  SJ-90B |  SJ-100B |  SJ-110B |  SJ-120B |
 Screw Diameter |  Φ90 |  Φ100 |  Φ110 |  Φ120 |
 Screw L/D Length | L/D 20:1-22:1 | |||
 Rational Speed of Screw Stem |  10-100r/min |  10-100r/min |  10-100r/min |  10-100r/min |
 Main Motor Power |  22kw |  22kw |  30kw |  37kw |
 Output |  70kg/h |  95kg/h |  120kg/h |  135kg/h |
 Weight of Overall(kg) |  2t |  2.1t |  2.2t |  2.5t |
 Cover Dimensions |  8000*1200*1800 |  8200*1600*1800 |  8500*1600*1800 |  8800*1600*1800 |
4. Machine Detail
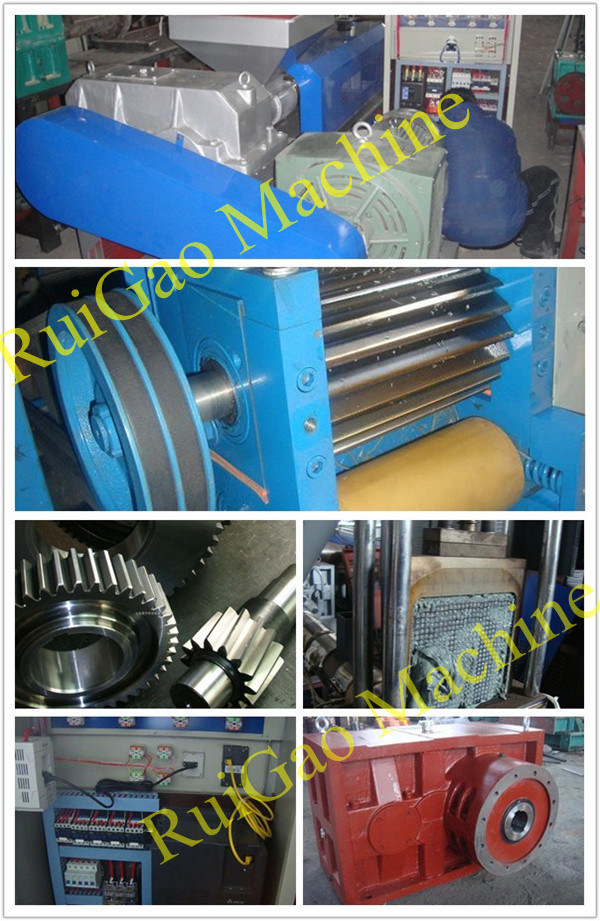
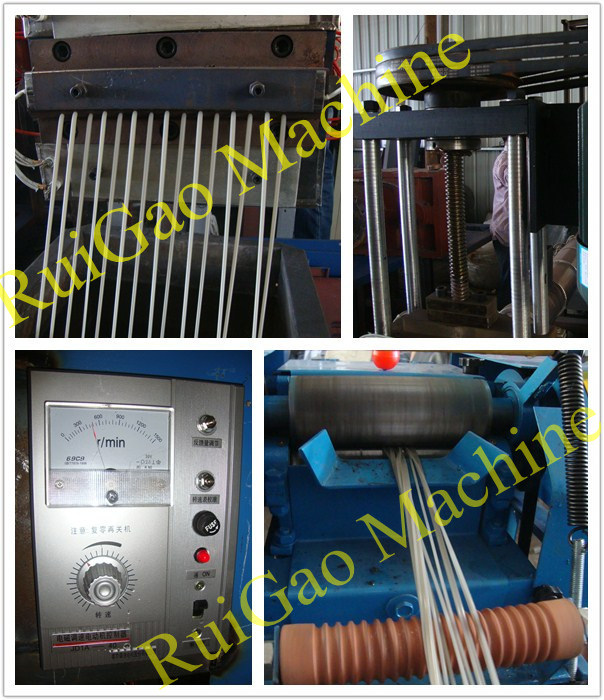
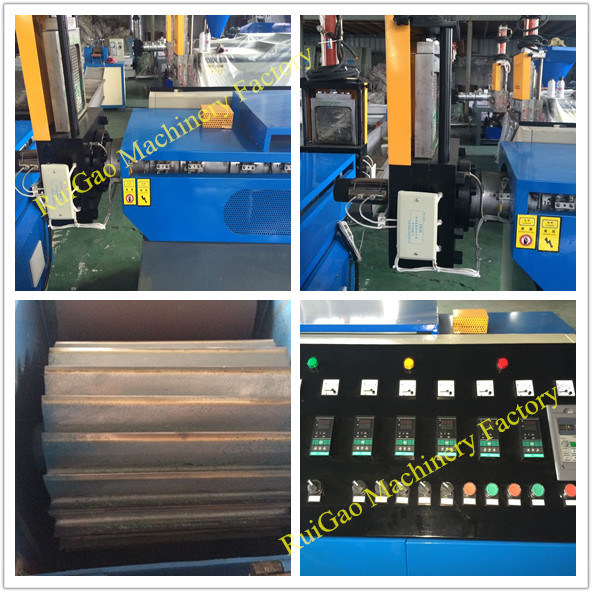
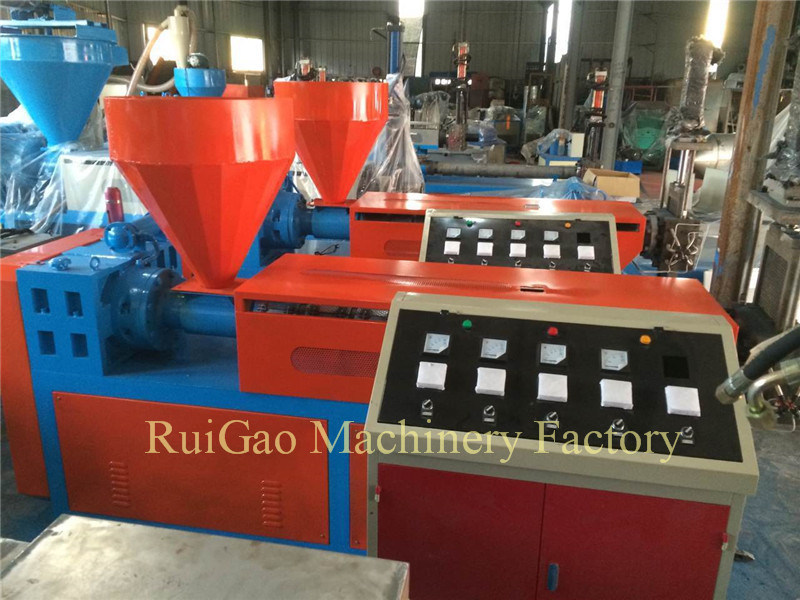
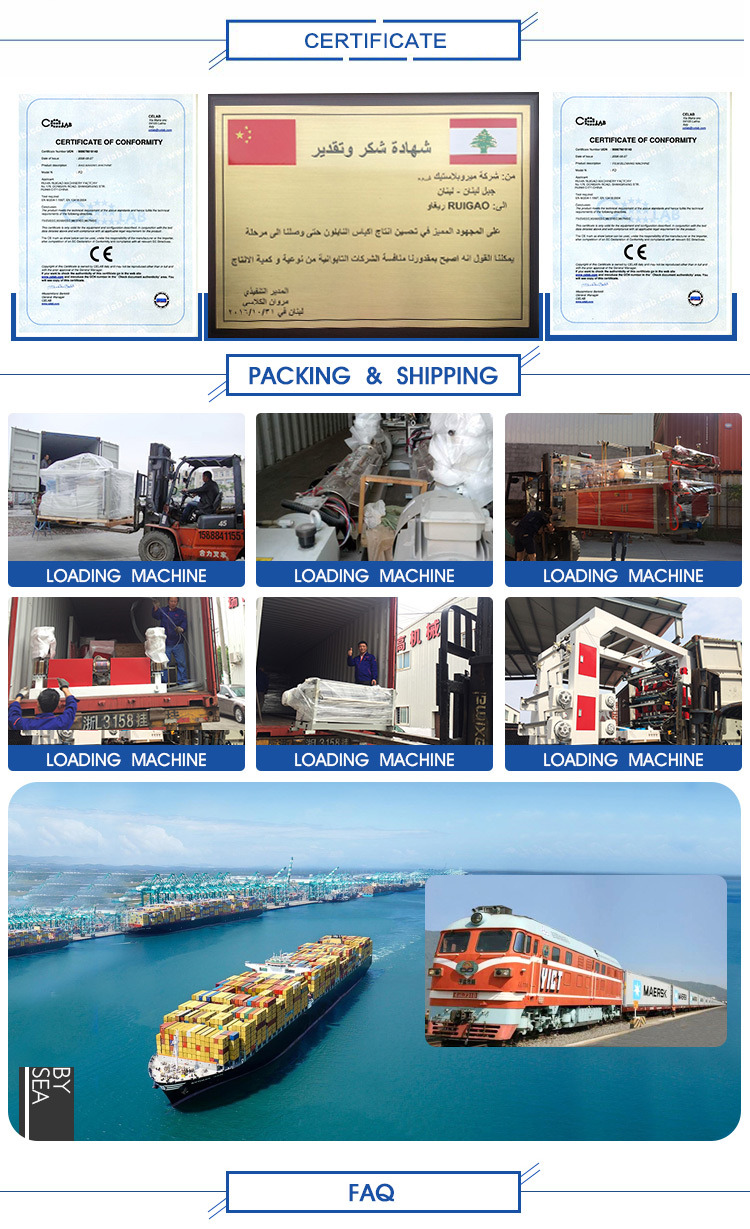
1,Q: Your factory is trading company or factory?
A: We are factory. We have more 2100 square meter workshop and 23 workers containing the 2 installment engineer and 1 electric engineer.
We are Factory, so we have cost advantage than Others
Â
2, Q: How do your company control the machine quality?
A: First we control the raw materials quality.
Second, we control the quality of machine when we are processing.
Third, Our installment engineer will test machine.
Â
3, Q: How about payment term, payment safety and delivery time?
A: We accept 30% deposit, balance before shipment. And Irrevocable L/C at sight.
Delivery time is 20 to 30 days. It is according to order quantity.
Â
4,Q: What is your company after sale service?
A: Our installment engineers are available. Normally it will take about 7 to 10 days for all.
Our guarantee is one year. If there is any spare parts is broken, we can send them freely to you.
You are welcome to contact with us, we will provide excellent quotation and high quality machine
Â
Â
The Die Castings that are created in this process can vary greatly in size and weight, ranging from a couple ounces to 100 pounds. One common application of die cast parts are housings - thin-walled enclosures, often requiring many ribs and bosses on the interior. Metal housings for a variety of appliances and equipment are often die cast. Several automobile components are also manufactured using die casting, including pistons, cylinder heads, and engine blocks. Other common die cast parts include propellers, gears, bushings, pumps, and Valves.
Die casting is a manufacturing process that can produce geometrically complex metal parts through the use of reusable molds, called dies. The die casting process involves the use of a furnace, metal, die casting machine, and die. The metal, typically a non-ferrous alloy such as aluminum or zinc, is melted in the furnace and then injected into the dies in the die casting machine. There are two main types of die casting machines - hot chamber machines (used for alloys with low melting temperatures, such as zinc) and cold chamber machines (used for alloys with high melting temperatures, such as aluminum). The differences between these machines will be detailed in the sections on equipment and tooling. However, in both machines, after the molten metal is injected into the dies, it rapidly cools and solidifies into the final part, called the casting. The steps in this process are described in greater detail in the next section.
Die cast parts can vary greatly in size and therefore require these measures to cover a very large range. As a result, die casting machines are designed to each accommodate a small range of this larger spectrum of values. Sample specifications for several different hot chamber and cold chamber die casting machines are given below.
Type | Clamp force (ton) | Max. shot volume (oz.) | Clamp stroke (in.) | Min. mold thickness (in.) | Platen size (in.) |
Hot chamber | 100 | 74 | 11.8 | 5.9 | 25 x 24 |
Hot chamber | 200 | 116 | 15.8 | 9.8 | 29 x 29 |
Hot chamber | 400 | 254 | 21.7 | 11.8 | 38 x 38 |
Cold chamber | 100 | 35 | 11.8 | 5.9 | 23 x 23 |
Cold chamber | 400 | 166 | 21.7 | 11.8 | 38 x 38 |
Cold chamber | 800 | 395 | 30 | 15.8 | 55 x 55 |
Cold chamber | 1600 | 1058 | 39.4 | 19.7 | 74 x 79 |
Cold chamber | 2000 | 1517 | 51.2 | 25.6 | 83 x 83 |
The selection of a material for die casting is based upon several factors including the density, melting point, strength, corrosion resistance, and cost. The material may also affect the part design. For example, the use of zinc, which is a highly ductile metal, can allow for thinner walls and a better surface finish than many other alloys. The material not only determines the properties of the final casting, but also impacts the machine and tooling. Materials with low melting temperatures, such as zinc alloys, can be die cast in a hot chamber machine. However, materials with a higher melting temperature, such as aluminum and copper alloys, require the use of cold chamber machine. The melting temperature also affects the tooling, as a higher temperature will have a greater adverse effect on the life of the dies.
Materials | Properties |
Aluminum alloys | ·Low density |
·Good corrosion resistance | |
·High thermal and electrical conductivity | |
·High dimensional stability | |
·Relatively easy to cast | |
·Requires use of a cold chamber machine | |
Copper alloys | ·High strength and toughness |
·High corrosion and wear resistance | |
·High dimensional stability | |
·Highest cost | |
·Low die life due to high melting temperature | |
·Requires use of a cold chamber machine | |
Zinc alloys | ·High density |
·High ductility | |
·Good impact strength | |
·Excellent surface smoothness allowing for painting or plating | |
·Requires such coating due to susceptibility to corrosion | |
·Easiest to cast | |
·Can form very thin walls | |
·Long die life due to low melting point | |
·Use of a hot chamber machine | |
Advantages: | ·Can produce large parts |
·Can form complex shapes | |
·High strength parts | |
·Very good surface finish and accuracy | |
·High production rate | |
·Low labor cost | |
·Scrap can be recycled |
Die Casting,Aluminum Die Casting,Die Casting Parts,Zinc Die Casting
Ningbo City Yinzhou Ruican Machinery Co.,Ltd , https://www.cnruican.com